Revolutionizing Tube Production
World-Class Manufacturing Facility
Located in the East of Gauteng Province, South Africa, our state-of-the-art facility specializes in high-quality multi-layer and mono-layer tubes for the oral care and cosmetic markets. Our 360-degree printing capabilities ensure stunning, full-coverage designs.
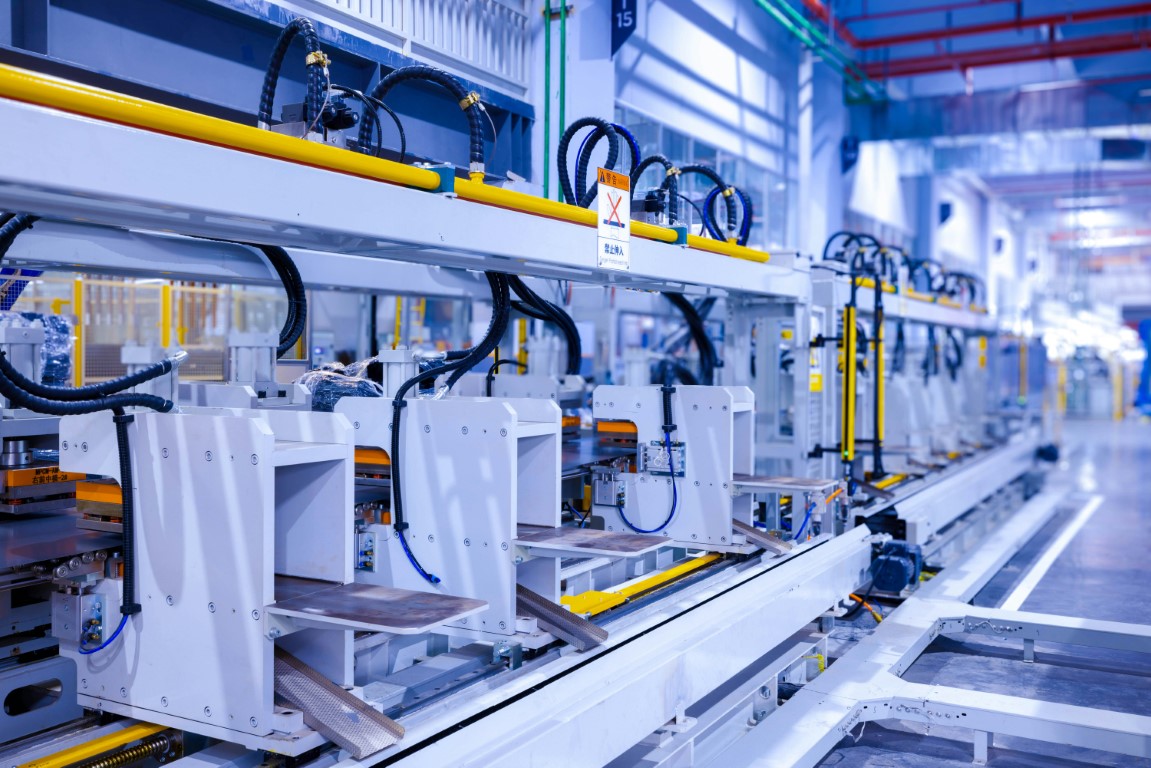
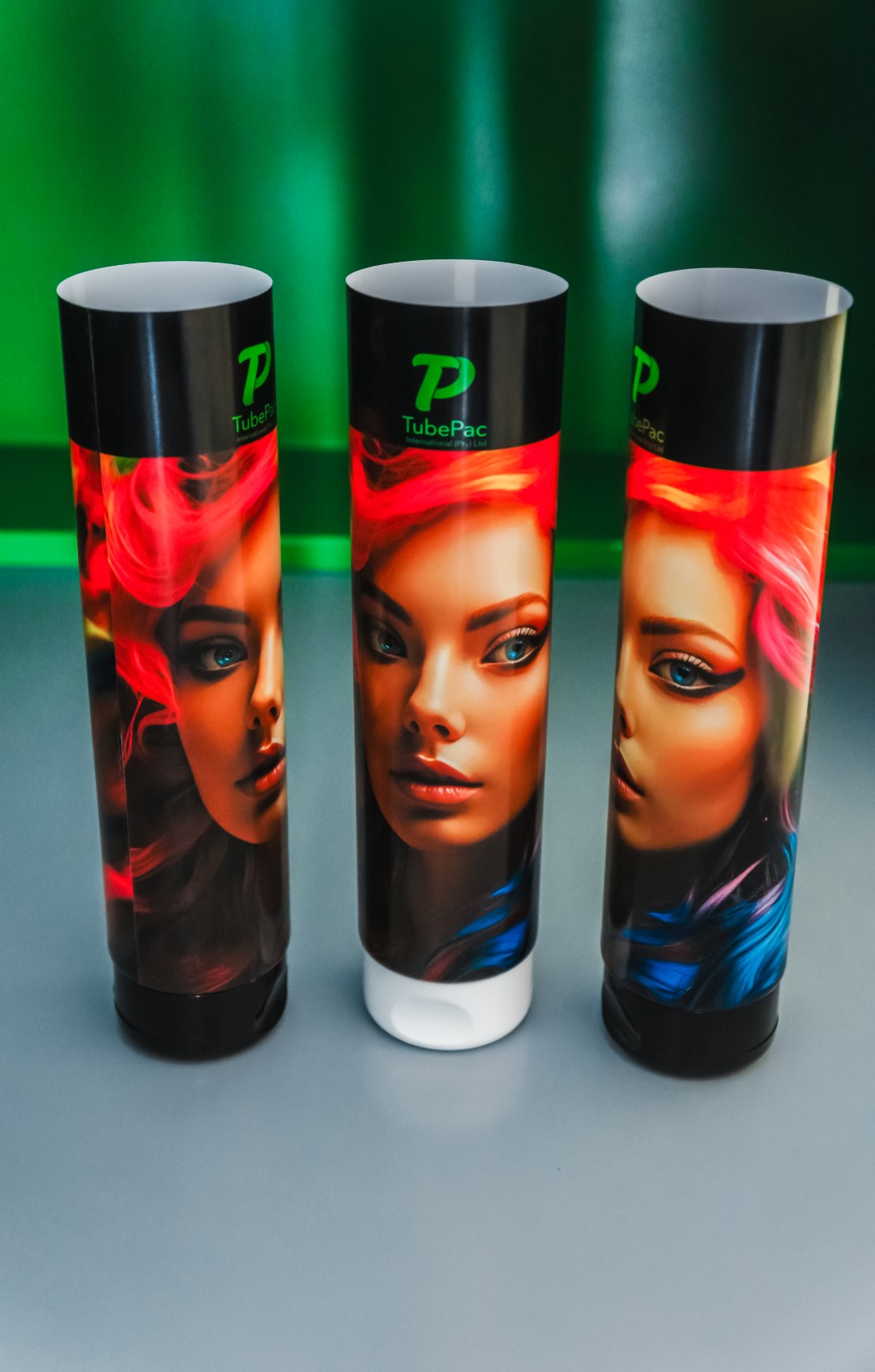
MPS EF-430 Press setting new benchmarks in tube decoration
Expanded Colour Gamut Flexographic Printing
Our Expanded Colour Gamut (ECG) flexographic printing technology delivers vibrant, high-quality prints with a wider color range, setting new benchmarks in tube decoration.
Acme Graphics, a leading provider of printing solutions, has partnered with TubePac to implement Expanded Colour Gamut (ECG) printing on the MPS EF430 press. This technology uses a fixed palette system (CMYK plus orange, green, and violet) to achieve high-quality, vibrant printing with a wider color range, enhancing the visual appeal and brand differentiation of TubePac’s products
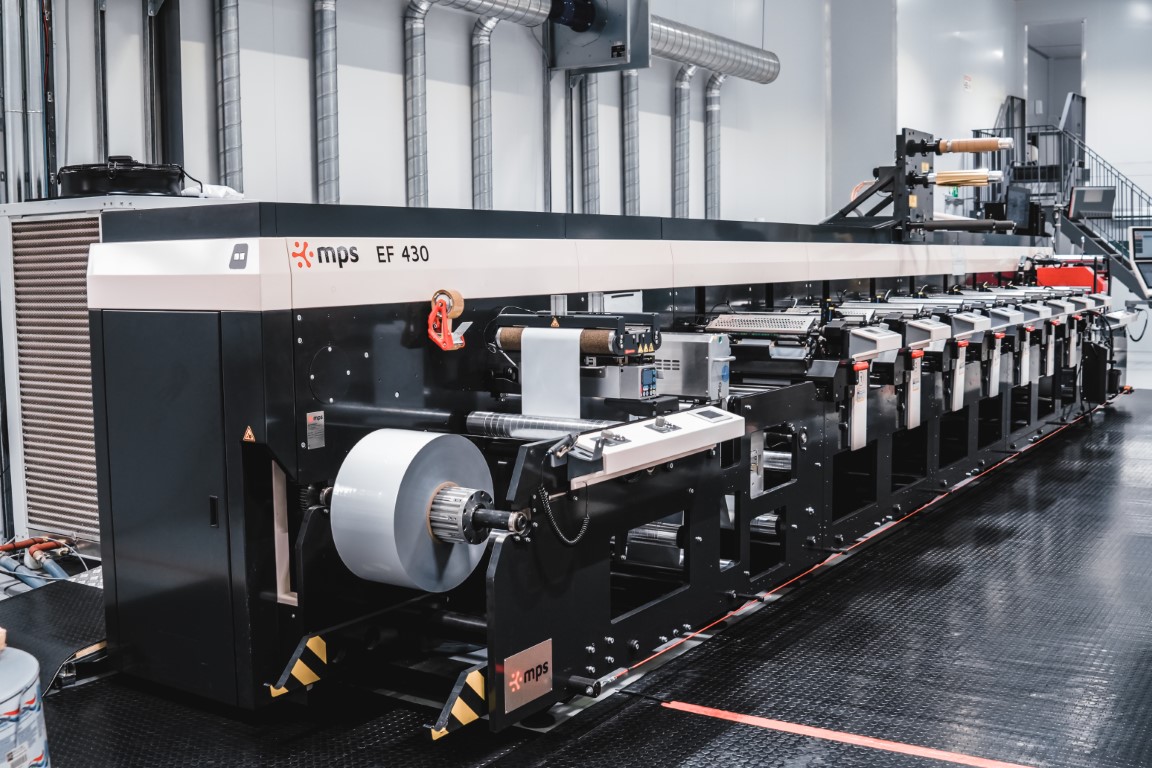
Rotocon and TubePac forming a strategic partnership
Read about Glenton Pick who moved mountains to establish TubePac International (Pty) Ltd in South Africa as a world-class multi-layer and mono-layer tube manufacturing facility with superior printing and fault detection capabilities, offering more sustainable alternatives for oral care and cosmetic product tubes.
High Quality, Vibrant Printing
MultiGamut® MPS EF430, single color system allows the press to utilize a fixed palette of seven primary colors (CMYK plus orange, green, and violet) to achieve a much wider color gamut compared to traditional CMYK printing. This results in more vibrant, accurate, and impactful colors on the tube surfaces.
Best-in-Class Print & Fault Detection
Delivering superior print quality, our technology ensures every tube stands out with crisp, clear, and vibrant graphics.
Best-in-Class Print Quality and Fault Detection
Our advanced print fault detection system ensures impeccable quality by identifying and correcting errors in real-time. This technology guarantees that every tube meets the highest standards of excellence.
Additionally, we have invested in an EyeC ProofRunner 100% inline inspection system and a ROTOCON CHROME RSI 430 slitter/rewinder, both connected via Quality Link workflow system software. This setup allows us to check and remove any detected defects in text, graphics, colour variations, variable data, or 1D and 2D codes, ensuring that our products meet the stringent quality standards demanded by the cosmetics and personal care sectors.
Our commitment to delivering exceptional tube packaging is realized through a combination of advanced technologies and meticulous processes:
1. MPS EF430 Flexo Press: This state-of-the-art printing press incorporates a range of features that contribute to superior print quality. These include:
- Multi-web functionalities: This allows for the printing of multiple layers of laminate material, ensuring consistent and accurate color reproduction.
- Stable web transport: This ensures that the material moves smoothly through the press, minimizing the risk of print defects.
- MPS Ultra-flex rail system: This allows for the integration of various converting modules, enabling TubePac to customize the printing process to meet specific product requirements.
- MPSConnect feature: This enables real-time data collection for all printing and operational related processes, allowing for continuous monitoring and optimization of print quality.
2. Acme Graphics’ MultiGamut® Single Colour System: This system enables TubePac to achieve Expanded Colour Gamut (ECG) printing on the MPS EF430 press. This technology allows for a wider color range and superior color accuracy, enhancing the visual appeal and brand differentiation of TubePac’s products.
3. EyeC ProofRunner 100% Inline Inspection System: This system is integrated into the production process to ensure that every printed tube meets the highest quality standards. The ProofRunner 100% inspects the printed material for any defects, including:
By investing in these advanced technologies and implementing meticulous quality control processes, TubePac International ensures that their tube packaging consistently meets the highest standards of print quality and fault detection. This commitment to excellence is crucial for building trust with customers and delivering products that meet the demanding requirements of the cosmetics and personal care industries.
AISA-100 Printing Machine
Forming Equipment
Our state-of-the-art forming equipment is designed to deliver precision and efficiency in tube manufacturing. This innovation enhances production speed and consistency, setting new industry benchmarks.
controlled setting minimizes contamination risks
Cleanroom Manufacturing Environment
Our state-of-the-art cleanroom manufacturing environment guarantees the highest standards of product quality and safety.
The cleanroom manufacturing environment is equipped with a live camera system that allows customers to remotely monitor the production process, ensuring transparency and the highest levels of product quality and safety.
This controlled setting minimizes contamination risks, ensuring that every tube meets stringent quality benchmarks.
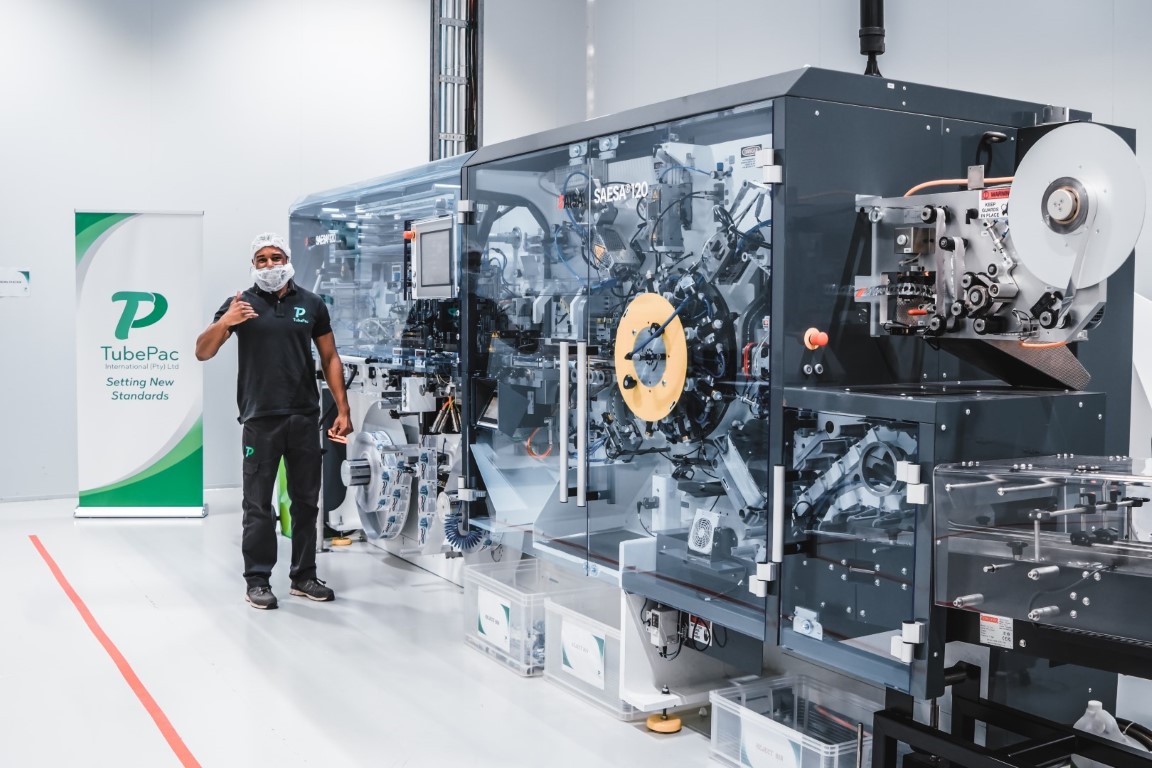
Streamlined, Integrated Tube Formation
Tube Slitting & Rewinding
Our advanced tube slitting and rewinding technology precisely cuts and rewinds materials, optimizing fault extraction. This innovation ensures that each tube is produced with impeccable accuracy and consistency.
While most tube manufacturers require separate machines for printing and forming the tubes, TubePac’s MPS EF430 press can handle both processes in a single, integrated workflow.
Our highly-customizable CHROME RSI 430 slitter/rewinder has been specified with an upgraded drive system to rewind tension-sensitive laminate materials at output rates of up to 320m/min, as well as an automatic slitting system to improve production efficiencies. The ECOLINE ultrasonic anilox roller cleaner quickly removes ink and dirt from any line count anilox cells, ensuring optimal print quality.
This not only improves efficiency but also ensures perfect alignment between the printed graphics and the physical tube components, delivering a premium, cohesive final product.